Metrology and
Calibration
The importance of
measurement
in our daily lives can not be overemphasized. Every new technology or
science breakthrough, industrial development, or commercial success
depends on one form of measurement or another. In these modern
times, we practically measure everything we encounter: the weight of our
food, the volume of our fuel, the distance between two points,
temperature, pressure, humidity, light, current, voltage, power, speed,
energy, etc.
Needless to say, reliable
measurement is very important to the semiconductor industry, or any
industry for that matter. In fact, it is so important that there's
already a science behind it. Known as
metrology,
it was developed and systematized to
ensure that all measurements performed are meaningful and according to
international standards.
After
all, one can not control or improve something that one can not measure,
and semiconductor manufacturing is one complex game of high-precision
control and continuous improvement.
Good measurement relies on the integrity of the
measuring equipment used. Unfortunately, no matter how sophisticated a
measuring equipment is, it degrades with time due to thermal,
mechanical, electrical, and environmental effects. This
degradation is called drift,
and it is unavoidable. However, the effects of drift on the
reliability of the measurements may be offset by a process known as
calibration.
Calibration
is simply the comparison of the measuring
instrument or equipment's performance to a reference standard of known accuracy.
In addition to this determination and reporting of
deviation from nominal, it may also include correction (adjustment) to minimize
the errors. Properly calibrated equipment provides confidence that the
company's products and services meet customer specifications
all over the world. In
the semiconductor industry, all critical equipment used in manufacturing
are required to undergo periodic calibration.
Another
commonly-encountered term in relation to calibration is verification.
Verification is not the same as
calibration because it refers to the comparison of the
measurement results against a specification, usually the manufacturer's published
performance figures for the product.
Calibration Traceability
The basic concept behind calibration is
that the measuring equipment should be tested against a standard of higher
accuracy. To illustrate this, below is a typical hierarchical
relationship among the various levels of calibration/measurement
activities within a company:
National Standard..........................
Accurate to 0.002%
Calibration
Laboratory........................................0.01 %
Company "Master"
Item.....................................0.07 %
Company Production
Equipment.........................1.0 %
Produced
Product............................................10.0 %
These calibrations need to be done on a planned,
periodic basis with evidence of the comparison results being recorded
and maintained. The records must include identification of the specific
standards used (which must be within their assigned calibration
interval), as well as the methods/conditions used in the calibration
process. These records should demonstrate an unbroken chain of
comparisons that ends at the agency responsible for maintaining
and developing a
country's measurement standards (now generically known as a
national metrology institute). This demonstrable linkage to national
standards, with known accuracy, is known as 'traceability'.
Periodicity
Periodicity refers to the
specified frequency of calibration or the regular interval between
calibrations defined for an equipment or a part thereof. The
periodicity depends on how quickly the equipment drifts out of spec,
what the equipment is for (is the application critical or not?), and
what the company can afford to do, but normally it ranges from 3 months
to 2 years. Periodicity may also be expressed as the
calibration cycle, which is the number of calibrations required per
year.
Characterization
Aside
from calibration which involves comparison of results against a standard
and possibly adjustment to nominal settings, a measuring equipment may
also be characterized. Characterization pertains to the evaluation or
study of parameters or properties which do not have specifications.
Characterization may be useful in determining the over-all limitations
and capabilities of the equipment.
Uncertainty
In
quantum physics, the 'Uncertainty Principle' states that the exact
position and exact velocity of a particle can not be determined at the
same time. Because of this, one can not measure something without
changing it. This
uncertainty principle very well applies to metrology and calibration,
i.e., every metrologist knows that there is no perfect measurement of
anything. An excellent metrologist would therefore consider all factors
affecting measurement uncertainty, and ensure that the total uncertainty
or inaccuracy of the measurement is less than the tolerance of the
specification for the parameter being measured.
Test
Accuracy Ratio
Test Accuracy Ratio, or TAR, is the ratio of the specification spec
of the parameter being measured to the uncertainty unc of
the measuring instrument, or TAR = spec/unc. Thus, the higher the TAR the better, but a higher TAR
will also cost more. The metrologist should therefore aim for the most
cost-effective TAR, i.e., the lowest TAR that will meet the company's
quality objectives.
Guardbanding
Low TAR's don't mean that the company has to erroneously accept actual
rejects as a result of measurement errors. Guardbanding is the process
of tightening the pass limits of the specification to account for the
uncertainty of the measuring equipment and other factors.
Guardbanding may reject some units that would otherwise be marginally
acceptable, but this is still better than shipping 'bad' products to the
customer.
Basic
Terminology
Accuracy - how close a measurement reading is to the
'true' value of the parameter being measured
Precision
- how repeatable or closely-grouped the measurement readings are
Resolution - the
level of discrimination that the measuring equipment can show; the
smallest unit change that it can discern or detect
Sensitivity - the smallest change in the input
(stimulus) that causes a discernible change in the output
Stability
- the tendency
of a measuring equipment not to 'drift' or degrade over time and usage
See Also:
Quality Systems;
Monitors and Controls;
Document Control;
The ISO9000 Standard;
Gage Repeatability and
Reproducibility
Books recommended for you: |
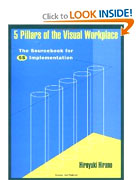 |
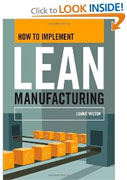 |
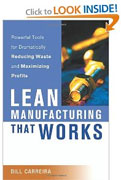 |
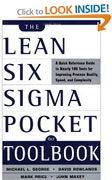 |
HOME
Copyright
© 2001
www.EESemi.com.
All Rights Reserved.